Proactive maintenance strategies create ripple effects throughout organizations, boosting profitability and operational resilience. Additionally, they enhance workplace safety by preventing hazardous equipment malfunctions.
Optimizing Manufacturing Processes with Digital Twins
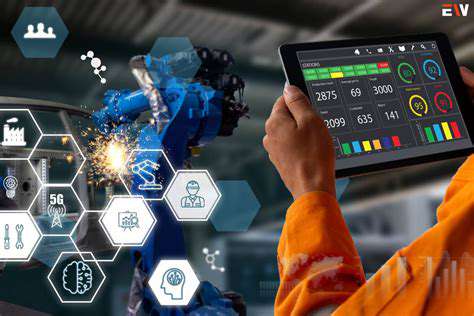
Streamlining Production Flow
Manufacturing optimization starts with comprehensive process mapping, identifying inefficiencies from raw materials to finished goods. Pinpointing workflow bottlenecks enables targeted improvements that accelerate throughput and minimize waste. Value stream analysis and lean methodologies help eliminate non-essential steps, creating more efficient production pathways.
Implementing 5S workplace organization principles further enhances flow by reducing motion waste and improving material accessibility. These combined approaches yield measurable productivity gains across manufacturing operations.
Improving Equipment Utilization
Maximizing machinery productivity requires balancing operational demands with preventive care. Synchronizing predictive maintenance with production schedules ensures equipment availability when needed most. Monitoring Overall Equipment Effectiveness (OEE) metrics helps identify underperforming assets for focused improvement.
Automation solutions complement human labor by handling repetitive tasks with precision and consistency. This dual approach of optimized maintenance and smart technology deployment creates a more responsive manufacturing environment.
Enhancing Quality Control
Building quality into manufacturing processes requires systematic approaches at every stage. Statistical Process Control (SPC) methods monitor production variables, enabling rapid detection of deviations. Cross-functional quality teams ensure standards permeate all organizational levels.
Digital inspection technologies augment traditional quality checks with real-time data capture and analysis. This fusion of human expertise and technological precision elevates product consistency while reducing defect rates.
Reducing Material Waste
Material efficiency strategies deliver both economic and environmental benefits. Lean inventory practices coupled with closed-loop recycling systems dramatically shrink waste streams while lowering costs. Process optimization minimizes scrap generation, while digital tracking ensures optimal material usage.
Just-in-time material delivery systems reduce storage needs and prevent obsolescence. These measures collectively contribute to more sustainable, cost-effective manufacturing operations.
Employee Training and Skill Development
Workforce capability directly impacts manufacturing performance. Continuous skills development creates adaptable teams capable of driving operational improvements. Cross-training enhances flexibility, while technology-specific instruction ensures proper equipment utilization.
Knowledge-sharing platforms and hands-on simulations accelerate competency development. Investing in human capital yields long-term dividends through improved productivity, innovation, and employee retention.
The Future of Digital Twins in Aerospace: Integration and Expansion
Integration with Existing Systems
The aerospace industry's digital transformation hinges on seamless digital twin integration with operational systems. Consolidated data streams from flight systems, maintenance records, and sensor networks create comprehensive aircraft profiles. This integration enables predictive analytics that optimize maintenance and operational decisions.
Extending connectivity to supply chain networks creates system-wide visibility. Parts procurement, inventory management, and logistics coordination benefit from this holistic approach, generating efficiency gains across the value chain.
Expanding Data Sources and Capabilities
Next-generation digital twins will incorporate diverse external data - weather patterns, air traffic conditions, and material performance metrics. This enriched data environment enables more accurate predictive modeling and risk assessment.
Advanced sensor networks will provide unprecedented visibility into structural integrity and system performance. These technological advancements will redefine maintenance strategies and operational protocols across the aerospace sector.
Real-Time Monitoring and Predictive Maintenance
Continuous digital twin monitoring transforms maintenance from scheduled to condition-based. Real-time performance tracking identifies degradation patterns early, preventing operational disruptions. This paradigm shift improves safety while reducing maintenance costs through optimized intervention timing.
Enhanced Simulation and Design
Virtual prototyping through digital twins accelerates development cycles while reducing physical testing costs. Engineers can explore design alternatives rapidly, evaluating performance under varied conditions. This simulation capability drives innovation while ensuring robust, reliable aerospace systems.
Improving Training and Education
Immersive training environments powered by digital twins provide realistic operational scenarios. Maintenance crews and flight personnel can practice complex procedures in risk-free virtual settings. This advanced preparation enhances workforce readiness and safety performance.
Optimization of Supply Chains and Logistics
Digital twin integration extends beyond aircraft to encompass entire supply networks. Predictive analytics optimize inventory levels, supplier coordination, and distribution logistics. This comprehensive visibility enables leaner, more responsive aerospace operations.
Security and Data Management
As digital twin networks expand, robust cybersecurity becomes paramount. Multi-layered protection strategies safeguard sensitive operational data while ensuring system integrity. Advanced encryption and access controls maintain data confidentiality across distributed networks.