Introduction to Modular Design in Spacecraft
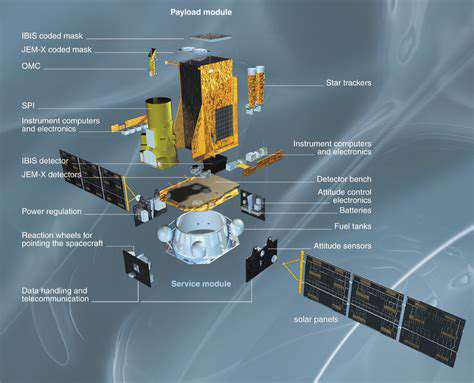
Understanding the Core Principles
At its core, modular design revolutionizes how we approach spacecraft engineering. Instead of monolithic structures, engineers now build systems using self-contained, swappable units. This paradigm shift enables teams to address intricate challenges through compartmentalized solutions, dramatically improving error containment and iterative refinement opportunities.
The fundamental philosophy centers on functional independence. Each component operates as a discrete entity with well-defined boundaries and standardized connection protocols. This architectural choice proves particularly valuable in extended operational scenarios where future-proofing through component upgrades becomes essential.
Benefits of a Modular Design Approach
The advantages of this methodology are numerous and impactful. Maintenance operations become exponentially simpler when technicians can isolate and replace malfunctioning units without dismantling entire systems, leading to substantial cost reductions and minimized operational interruptions. The plug-and-play nature of components also accelerates both repair procedures and technology refresh cycles.
System evolution benefits tremendously from this architecture. Engineers can introduce cutting-edge technologies through module swaps rather than complete system redesigns. This adaptability proves indispensable for missions expected to remain operational through multiple technology generations.
Modular Design in Software Development
The software domain mirrors these hardware advantages through component-based architectures. Developers encapsulate discrete functionalities - whether data processing routines, control algorithms, or interface elements - into independent software modules. This organizational strategy yields cleaner, more maintainable codebases.
Debugging and enhancement processes benefit enormously from this separation. Software teams can modify individual components without triggering cascading changes throughout the system, a critical advantage for complex, long-lived spacecraft software systems requiring continuous improvement.
Challenges in Implementing Modular Design
Despite its advantages, the approach presents implementation hurdles. Interface standardization demands meticulous attention, as inconsistent connection protocols can undermine the entire system's reliability. The interdependency management between numerous autonomous units requires sophisticated coordination strategies.
System architects must carefully balance modular independence with overall system cohesion. Achieving this equilibrium demands comprehensive planning and rigorous testing protocols to ensure seamless module integration and operation.
Applications Across Various Industries
This design philosophy transcends aerospace applications. Automotive manufacturers employ modular platforms for everything from electric vehicle battery systems to autonomous driving components. Consumer electronics companies leverage modularity for customizable user experiences and sustainable product lifecycles.
In medical technology, modular systems enable personalized treatment solutions through configurable component arrangements, particularly in advanced imaging systems and robotic surgical platforms. This flexibility proves vital in fields demanding precision customization for diverse operational requirements.
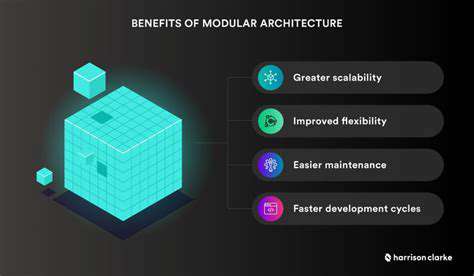
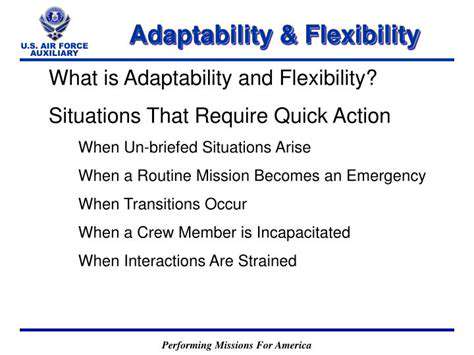
Cost-Effectiveness and Reduced Development Time
Modular Design for Optimized Costs
Spacecraft budgets benefit dramatically from modular architectures. Standardized component libraries eliminate redundant design efforts, while mass production of common modules drives down per-unit costs. The economic advantages extend throughout the product lifecycle, as maintenance and upgrades become substantially more affordable compared to integrated designs.
Operational resilience improves through this approach. Mission controllers can replace malfunctioning orbital units with pre-qualified spares, avoiding costly complete system failures and mission abort scenarios.
Reduced Development Time Through Component Reusability
Schedule compression represents another major benefit. Space agencies can assemble new spacecraft configurations from flight-proven building blocks, bypassing years of qualification testing typically required for novel designs. This accelerated development pathway enables more frequent mission opportunities within constrained budget cycles.
Improved Scalability and Adaptability
The architecture's inherent flexibility supports mission evolution. Scientific teams can augment observation capabilities by integrating new instrument modules during servicing missions. This dynamic reconfigurability proves invaluable for long-duration missions where scientific priorities may shift during the operational phase.
Mission planners gain unprecedented flexibility to repurpose spacecraft for alternative objectives through module swaps. This capability provides insurance against changing political priorities or unexpected scientific discoveries that warrant investigation.
Simplified Manufacturing and Logistics
Production processes benefit from parallelized module manufacturing. Specialized facilities can focus on perfecting specific component types, while standardized interfaces ensure seamless system integration. The supply chain simplifies through reduced part variety and established qualification protocols for modular components.
Enhanced Maintainability and Upgradability
Orbital servicing becomes practical through modular architectures. Astronauts or robotic systems can replace aging components with improved versions, extending spacecraft utility far beyond original design lifetimes. This approach revolutionizes asset management in the space domain, transforming spacecraft from disposable assets into upgradable platforms.
Potential for Enhanced Safety and Reliability
Flight heritage accumulates faster with reusable modules. Each successful mission provides additional validation for component designs, creating a virtuous cycle of reliability improvement. The ability to isolate and contain failures within individual modules provides additional layers of system redundancy and fault tolerance.