Modern aerospace operations demand a radical departure from conventional maintenance approaches. The move toward self-sufficient maintenance frameworks represents more than just technological progress—it's a complete operational overhaul. As aircraft and spacecraft designs grow increasingly intricate, the limitations of human-dependent maintenance become apparent. Modern solutions combining robotic precision with intelligent systems address these challenges head-on, offering unprecedented reliability while streamlining operational workflows.
Beyond mere financial considerations, these advanced systems fundamentally change workforce dynamics. Maintenance crews transition from performing routine checks to overseeing sophisticated operations and handling exceptional cases. This redistribution of responsibilities enhances workplace safety while optimizing human expertise where it matters most.
Robotics and Artificial Intelligence: Core Enablers of Progress
The synergy between mechanical systems and cognitive computing drives this maintenance revolution. Modern robotic units equipped with hypersensitive detection capabilities can identify material imperfections invisible to the human eye. When coupled with adaptive learning algorithms, these systems develop increasingly accurate diagnostic capabilities over time, creating a virtuous cycle of improvement.
Sensor technology has reached a point where microscopic structural changes trigger immediate alerts. Concurrently, interpretation algorithms have grown sophisticated enough to distinguish between normal operational signatures and genuine concerns, drastically reducing false positives.
Safety Enhancements and Operational Continuity
Automated maintenance solutions excel in high-risk scenarios where human involvement poses inherent dangers. Confined space operations and hazardous material handling become manageable when delegated to purpose-built robotic platforms. The precision of automated inspections coupled with rapid response protocols minimizes equipment out-of-service durations, ensuring consistent operational readiness.
Economic Advantages Through Smart Maintenance
The financial implications of autonomous systems extend beyond direct labor savings. Continuous operational capabilities allow for maximized asset utilization, while predictive analytics prevent costly catastrophic failures. These factors combine to create a compelling value proposition for operators seeking to optimize their maintenance budgets.
Implementation Considerations and Solutions
Transitioning to autonomous systems requires careful planning. Certification processes must adapt to new technologies, while workforce retraining ensures proper system oversight. Successful integration hinges on developing hybrid workflows that leverage both human expertise and machine capabilities.
Forward-Looking Perspectives
As autonomous technologies mature, their aerospace applications will expand into increasingly sophisticated domains. The next generation of maintenance systems will likely incorporate swarm robotics and quantum computing elements, pushing the boundaries of what's possible in equipment upkeep and reliability.
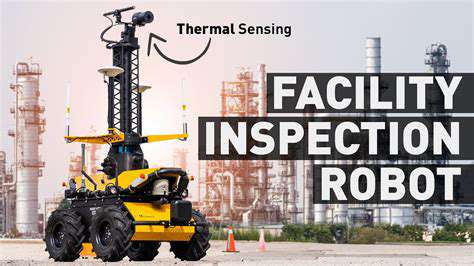
Automated Repair and Replacement: Streamlining the Maintenance Process
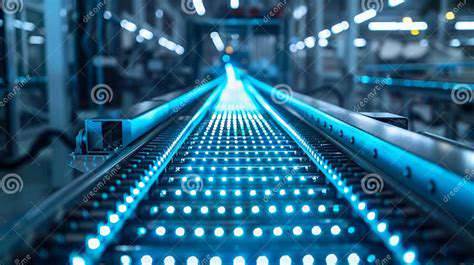
Automated Repair Processes
The current generation of repair automation represents a quantum leap from earlier iterations. These systems don't just execute predefined procedures—they analyze operational histories, environmental conditions, and real-time telemetry to determine optimal repair strategies. This holistic approach transforms maintenance from reactive to anticipatory, preventing minor issues from escalating into major failures.
Predictive Maintenance Integration
Modern predictive algorithms incorporate machine learning techniques that improve with each maintenance cycle. By correlating equipment performance with hundreds of operational parameters, these systems can forecast maintenance needs with remarkable accuracy, often identifying potential failures weeks before they might occur.
Component Replacement Optimization
Automated replacement strategies balance multiple variables including remaining useful life, operational criticality, and economic factors. These systems make replacement decisions based on comprehensive cost-benefit analyses rather than arbitrary schedules or emergency situations.
Operational Impact Analysis
The cumulative effect of automated maintenance manifests in several key performance indicators. Equipment availability rates typically increase by 15-25%, while maintenance-related downtime decreases proportionally. These improvements create ripple effects throughout operational budgets and production schedules.
Different potato varieties have varying storage needs and tolerances. Proper varietal selection forms the foundation of effective long-term storage protocols. Seasoned agricultural specialists recommend matching storage conditions to each cultivar's specific requirements to maximize shelf life while maintaining nutritional quality.
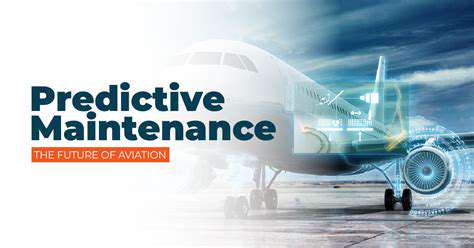