Computational Fluid Dynamics (CFD) in the Design Process
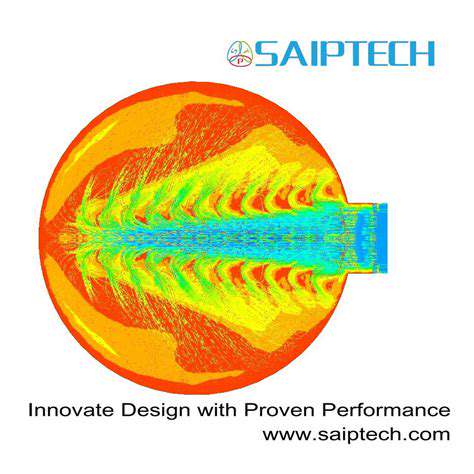
Introduction to CFD
Computational Fluid Dynamics (CFD) is a powerful tool used to simulate fluid flow, heat transfer, and other related phenomena. It allows engineers and scientists to analyze complex fluid systems without the need for expensive and time-consuming physical experiments. This approach provides a valuable alternative for understanding and optimizing designs in various industries, from aerospace to biomedical engineering.
Applications of CFD
CFD has a wide range of applications across numerous industries. In the automotive industry, CFD is used to optimize vehicle aerodynamics, reducing drag and improving fuel efficiency. It also helps in designing efficient cooling systems and optimizing engine performance.
Beyond automotive, CFD is crucial in the aerospace industry for designing aircraft wings, engines, and other components. It also plays a significant role in the design of pipelines, pumps, and other industrial equipment.
Methodology and Techniques
CFD simulations rely on mathematical models and numerical methods to solve the governing equations of fluid mechanics. These equations, such as the Navier-Stokes equations, describe the conservation of mass, momentum, and energy within a fluid.
Various discretization techniques, such as finite volume and finite element methods, are employed to convert these complex equations into a form suitable for numerical computation. These numerical methods allow for the solution of these equations within a computational domain, providing insights into the flow patterns and characteristics.
Challenges and Limitations
Despite its power, CFD simulations come with certain limitations. The accuracy of the results is heavily dependent on the quality of the numerical methods employed and the choice of boundary conditions. The computational resources required for complex simulations can also be substantial. Furthermore, accurately representing real-world phenomena like turbulence and multiphase flows can be challenging, sometimes requiring sophisticated turbulence models and advanced numerical techniques.
Choosing appropriate turbulence models and grid resolution is crucial for obtaining reliable results. Ignoring these factors can lead to significant errors in the prediction of flow characteristics.
Software and Tools
Several commercial and open-source CFD software packages are available, offering a wide range of functionalities and capabilities. These tools provide pre- and post-processing capabilities, enabling users to define the computational domain, specify boundary conditions, and visualize the simulation results. Fluent, ANSYS CFX, and OpenFOAM are examples of popular CFD software packages used by professionals.
These tools allow users to manipulate and visualize the data, enabling a deeper understanding of the simulated flow. Effective use of these tools is crucial for accurate and insightful results.
Shape Optimization and Surface Roughness
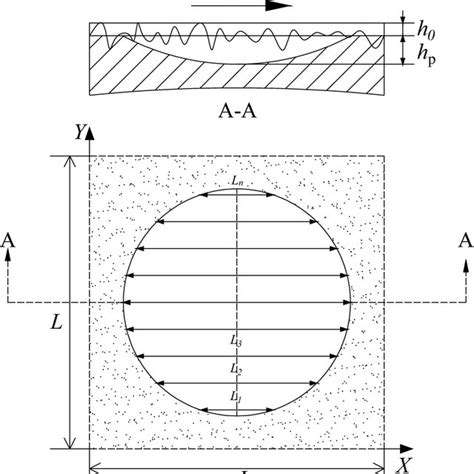
Shape Optimization Techniques
Shape optimization is a crucial aspect of modern design, enabling engineers to create components with enhanced performance and reduced material usage. This process involves systematically altering the geometry of a design to improve specific characteristics, such as strength, stiffness, and aerodynamic efficiency. Iterative computational methods are commonly employed to refine the shape, ensuring the desired characteristics are met while minimizing material waste. Advanced algorithms consider various constraints and objectives, allowing for the creation of optimized solutions.
Different techniques exist, ranging from simple parametric modeling to sophisticated topology optimization. These methods use mathematical models to evaluate the design's performance under different conditions and then modify the shape accordingly. The selection of the appropriate technique depends heavily on the complexity of the design and the specific performance goals.
Surface Roughness Considerations
Surface roughness plays a critical role in the performance and longevity of manufactured components. Uneven surfaces can lead to increased friction, reduced wear resistance, and compromised aesthetic appeal. Understanding and controlling surface roughness is essential for achieving desired functionality and quality.
Surface roughness is often quantified using parameters like Ra (average roughness) and Rz (maximum height). Careful consideration of these parameters during the design and manufacturing process is vital for ensuring the part meets the required specifications. Different manufacturing processes produce different surface finishes, and the choice of process directly impacts the final roughness.
Material Selection Impact
The choice of material significantly impacts the design process and the final characteristics of the optimized shape. Different materials exhibit varying degrees of strength, stiffness, and ductility. Selecting the appropriate material for a given application ensures that the optimized shape can withstand the anticipated stresses and loads. This selection is often influenced by the desired performance characteristics and the manufacturing constraints.
Manufacturing Process Integration
Optimizing a shape is not complete without considering the manufacturing process. The chosen manufacturing method directly influences the feasibility and cost of producing the optimized design. Different processes have different capabilities in terms of achieving the desired surface finish and tolerances. For example, 3D printing can handle complex geometries, while traditional machining may be better suited for simpler shapes. A holistic approach that integrates shape optimization with manufacturing process constraints is essential for creating practical and cost-effective designs.
Design Constraints and Objectives
Shape optimization is not a free-form exercise. Real-world designs are governed by numerous constraints, including material limitations, manufacturing tolerances, and functional requirements. Engineers must carefully define these constraints and objectives to guide the optimization process effectively. These constraints can include specific weight limits, allowable stress levels, and dimensional accuracy requirements.
Clear definition of the desired performance characteristics is vital. This could involve factors like load-bearing capacity, heat dissipation, or aerodynamic performance, to name a few. These objectives are critical to focusing the optimization process toward achieving the best possible outcome.
Computational Tools and Software
Advanced computational tools and software play a critical role in performing shape optimization. These tools provide the computational power and algorithms necessary for evaluating numerous design variations and identifying optimal solutions. These programs often incorporate finite element analysis (FEA) to simulate the behavior of the component under different loading conditions. Sophisticated software allows engineers to effectively explore the design space and identify trade-offs between various design parameters.
The use of these tools enables efficient exploration of a large design space, accelerating the design process. The outputs from these simulations provide valuable insights into the performance and behavior of the design under different conditions. This ability to simulate and analyze enables engineers to make informed decisions and optimize the design iteratively.
Advanced Optimization Techniques and Materials
Finite Element Analysis (FEA)
Finite element analysis (FEA) is a powerful computational method used to simulate the behavior of complex structures under various loading conditions. In aerodynamic optimization, FEA allows engineers to analyze stress, strain, and deformation of aircraft components, such as wings and fuselage, subjected to aerodynamic forces and moments. This analysis is crucial for identifying potential failure points and optimizing material selection and structural design for enhanced strength and durability while maintaining lightweight construction.
By simulating different design scenarios within FEA software, engineers can evaluate the performance of various materials and geometries. This iterative process allows for the identification of optimal designs that meet the required strength, stiffness, and weight criteria, ultimately leading to improved aerodynamic performance.
Computational Fluid Dynamics (CFD)
Computational fluid dynamics (CFD) is a computational method used to analyze and predict fluid flow, including air flow around aircraft. CFD simulations provide detailed insights into the aerodynamic characteristics of different designs, such as lift, drag, and pressure distributions. This data is invaluable in identifying areas of high pressure drag and low pressure lift, enabling engineers to optimize the shape and configuration of aircraft components for improved aerodynamic performance.
Sophisticated CFD techniques, combined with advanced meshing strategies, allow for precise modeling of complex flow phenomena, such as turbulence and boundary layers. This detailed analysis enables the identification of aerodynamic inefficiencies and the development of optimized designs that minimize drag and maximize lift.
Topology Optimization
Topology optimization is a design methodology that explores a wide range of possible geometries within a given design space. By using computational algorithms, it identifies the optimal material distribution within a structure to maximize performance criteria, such as strength, stiffness, or aerodynamic efficiency. This technique is particularly useful in exploring unconventional designs and discovering innovative solutions for aerodynamic challenges.
Topology optimization algorithms evaluate the performance of various material distributions within a given volume. They iteratively refine the design, removing or adding material in specific areas based on the computational results. This iterative process helps to discover designs that are both lightweight and highly efficient in terms of aerodynamic performance.
Multi-objective Optimization
Aircraft design often involves conflicting objectives, such as minimizing drag, maximizing lift, and reducing weight. Multi-objective optimization techniques enable engineers to simultaneously address these competing objectives and identify designs that achieve a good balance between them. This approach is crucial for achieving optimal aerodynamic performance while considering other critical design constraints.
Multi-objective optimization algorithms generate a set of Pareto-optimal solutions, each representing a different trade-off between the objectives. Engineers can then select the design that best suits the specific requirements and priorities of the aircraft application.
Material Selection and Characterization
The choice of materials plays a significant role in aerodynamic optimization. Different materials possess varying properties, including density, strength, stiffness, and thermal conductivity. Selecting appropriate materials is vital for achieving the desired balance between weight reduction, structural integrity, and thermal management. Advanced characterization techniques, such as experimental testing and material modeling, are employed to evaluate the performance of different materials under various aerodynamic conditions.
Careful consideration of material properties, such as fatigue resistance and damage tolerance, is essential for ensuring the longevity and reliability of the aircraft. This approach ensures that the optimized design will meet the required standards for safety and performance throughout the aircraft's operational lifespan.