The Dawn of Customized Aerospace Components
Additive Manufacturing's Impact on Aerospace Component Design
The emergence of additive manufacturing (AM), commonly called 3D printing, is transforming aerospace production. This approach facilitates crafting intricate, bespoke parts with unparalleled design flexibility, shattering previous constraints. AM liberates engineers from traditional manufacturing shackles, enabling revolutionary designs that perfect weight distribution, durability, and operational efficiency.
Customizing for Enhanced Performance
Unlike conventional techniques, AM produces complex geometries that were formerly unfeasible or cost-prohibitive. This breakthrough yields remarkable performance gains. Designers can incorporate internal cooling systems precisely calibrated for thermal management, or sophisticated support structures that maximize strength while conserving materials. Such meticulous control results in components fine-tuned for exact operational demands.
Material Selection and Design Flexibility
Aerospace applications demand specific material characteristics for safety and performance. AM accommodates diverse materials including advanced alloys, composite substances, and specialized polymers. This versatility expands creative possibilities, allowing components with exceptional property combinations like high durability paired with minimal weight.
Reduced Manufacturing Costs and Time
Although AM machinery requires significant upfront investment, the technology delivers undeniable long-term advantages. By simplifying production and frequently removing intricate tooling needs, AM shortens development cycles and accelerates component availability. This efficiency benefits both prototyping and full-scale manufacturing.
Improved Component Integration and Reduced Weight
AM permits direct incorporation of functional elements like fasteners within components themselves. This consolidation decreases part quantities, simplifies assembly, and lowers overall mass. In aviation applications, such weight reductions directly enhance fuel economy and aircraft performance.
Addressing the Challenges of Certification and Validation
Despite its benefits, AM adoption faces aerospace industry certification hurdles. Establishing rigorous testing standards remains critical for widespread implementation. Current research focuses on developing reliable validation methods to ensure AM components meet stringent safety requirements, fostering industry confidence in these advanced manufacturing techniques.
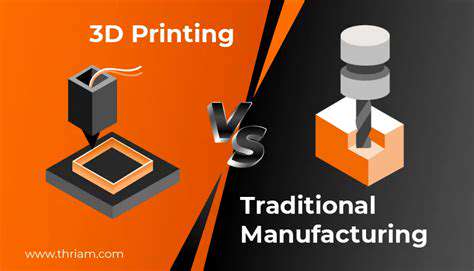
Enhanced Design Freedom and Prototyping Speed
Enhanced Design Freedom
Additive manufacturing revolutionizes aerospace design by overcoming traditional production limitations. The technology facilitates creation of lightweight, complex configurations impossible through conventional means. Engineers enjoy expanded creative possibilities, pushing aerodynamic and functional boundaries to develop more efficient aircraft systems. The capacity to embed intricate internal frameworks optimizes strength while reducing mass, yielding substantial fuel savings.
Faster Prototyping Cycles
AM dramatically compresses prototype development timelines. Rapid iteration allows engineers to evaluate multiple configurations quickly, refining designs before committing to production tooling. This accelerated process reduces development costs and shortens market introduction for new aviation technologies. Functional prototypes enable comprehensive validation, minimizing costly trial-and-error approaches.
Material Exploration and Optimization
The technology enables unprecedented material experimentation for aerospace applications. From high-performance alloys to advanced polymers, AM accommodates diverse substances tailored to specific requirements. This flexibility permits property customization for enhanced durability and reduced maintenance. Multi-material integration within single components, difficult with traditional methods, further elevates performance capabilities.
Improved Component Integration
AM excels at creating sophisticated parts that interface seamlessly with existing systems. This proves particularly valuable in aviation where integrated components optimize performance and weight distribution. The technology allows direct incorporation of sensors, wiring, and other functional elements, reducing assembly complexity and improving aerodynamic efficiency.
Reduced Manufacturing Costs
While initial AM equipment investments are substantial, long-term savings materialize through eliminated tooling expenses and minimized secondary operations. The technology proves especially cost-effective for low-volume production of specialized components. Single-step fabrication of complex geometries reduces processing stages, generating significant production efficiencies.
Sustainability Considerations
AM presents environmental advantages through material conservation and waste reduction. On-demand production with minimal excess aligns with sustainable manufacturing principles. Emerging use of recycled and bio-based materials further enhances ecological benefits, addressing growing industry demands for environmentally responsible solutions.
Material Innovation and Performance Enhancement
Material Innovation in Additive Manufacturing
AM drives aerospace material advancement beyond geometric complexity. The technology enables novel material combinations and microstructural optimization, fostering development of lighter, more resilient components. Researchers are investigating advanced metallic alloys, high-temperature polymers, and specialized ceramics, each processed for optimal performance in demanding flight conditions.
Enhanced Component Performance Through Design Optimization
Unprecedented design freedom allows creation of components with optimized internal architectures. Strategic use of lattice structures and selective reinforcement achieves superior mechanical properties while conserving material. This precise engineering approach yields weight reductions critical for fuel efficiency and environmental impact reduction.
Improved Durability and Reliability
AM facilitates intricate internal features that enhance component longevity. These designs distribute mechanical stresses more evenly, inhibiting crack formation and propagation. The technology's precise material deposition enables tailored microstructures resistant to corrosion and extreme environments, extending service life and reducing maintenance requirements.
Surface Finish and Surface Treatment Enhancements
While AM produces complex geometries, surface quality remains crucial for aerospace applications. Parameter optimization and post-processing techniques improve finish characteristics critical for coating adhesion and operational performance. Ongoing advancements address surface roughness challenges inherent in some AM processes.
Material Selection for Specific Applications
The extensive AM material portfolio enables precise matching of properties to application demands. Titanium alloys serve in critical structural applications, while specialized polymers suit less demanding environments. This targeted material selection ensures optimal performance across diverse aerospace applications, from airframes to propulsion systems.
Cost-Effectiveness and Manufacturing Efficiency
AM delivers long-term economic benefits despite initial capital requirements. Digital manufacturing minimizes waste and eliminates expensive tooling, particularly advantageous for customized or low-volume components. Rapid prototyping capabilities accelerate development cycles, providing competitive advantages in time-sensitive aerospace markets.
Future Directions and Research Areas
Ongoing AM research focuses on novel materials, hybrid manufacturing techniques, and advanced simulation tools. These developments aim to further enhance component performance while reducing production costs. Computational design optimization will play an increasingly important role in creating next-generation aerospace components that push performance boundaries.
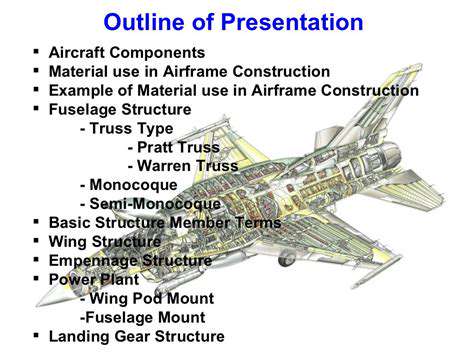