The transition from reactive to predictive maintenance represents one of the most significant operational improvements in modern industry. Rather than waiting for equipment failures to occur, AI systems can anticipate issues before they manifest. This proactive approach delivers measurable benefits by minimizing unplanned downtime and extending equipment service life.
Advanced analytics capabilities allow these systems to process complex data from multiple sources, including sensor networks, maintenance logs, and operational parameters. Through continuous analysis, the algorithms develop increasingly accurate models of equipment behavior and failure patterns.
Data Collection and Analysis: The Foundation
Effective predictive maintenance relies on comprehensive data collection systems. Strategically positioned sensors monitor critical parameters including vibration frequencies, thermal patterns, pressure variations, and electrical characteristics. The quality and consistency of this data directly impacts the reliability of predictive analyses. When combined with historical maintenance records, this information forms the basis for highly accurate predictive models.
Machine Learning Algorithms: The Engine
At the core of predictive maintenance systems are sophisticated machine learning models that continuously analyze operational data. These algorithms identify subtle patterns and correlations that might escape human detection. Over time, their predictive capabilities become increasingly precise through ongoing learning processes.
Different algorithmic approaches - including regression analysis, classification methods, and anomaly detection techniques - work in concert to assess equipment health. This multi-faceted analysis enables maintenance teams to prioritize tasks and allocate resources with maximum efficiency.
Predicting Failures: Anticipating the Unexpected
The true value of predictive systems lies in their ability to forecast potential failures with remarkable accuracy. These predictions often include estimated timeframes, allowing maintenance scheduling with optimal lead times. Such foresight proves invaluable for maintaining continuous operations while minimizing disruption to production schedules.
By addressing potential issues during planned maintenance windows, organizations can avoid the substantial costs and operational impacts associated with unexpected equipment failures.
Optimizing Maintenance Schedules: Efficiency and Cost Savings
Predictive maintenance enables a fundamental shift from calendar-based to condition-based maintenance strategies. Instead of performing routine maintenance regardless of actual need, interventions occur precisely when warranted by equipment condition. This optimized approach reduces unnecessary maintenance while ensuring critical repairs receive timely attention.
The financial benefits of this methodology extend beyond immediate repair cost savings to include extended equipment lifespan and improved operational efficiency throughout the asset lifecycle.
Real-World Applications and Benefits: Transforming Industries
Across industries ranging from manufacturing to energy production, predictive maintenance systems demonstrate consistent value. Early adopters report significant improvements in operational reliability coupled with reduced maintenance expenditures. The combination of lower costs and improved equipment availability creates compelling business cases for implementation.
These systems not only prevent costly breakdowns but also contribute to more sustainable operations by minimizing unnecessary part replacements and resource consumption.
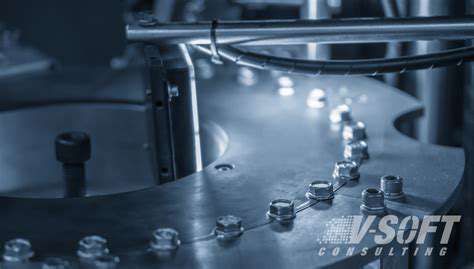
AI-Driven Automation in Manufacturing Processes
Improving Efficiency and Productivity
The integration of AI into manufacturing operations delivers substantial efficiency gains across production processes. By analyzing data streams from equipment sensors, production logs, and supply chain systems, intelligent algorithms identify optimization opportunities that might otherwise remain hidden. This analytical capability enables manufacturers to streamline workflows, reduce cycle times, and maximize equipment utilization.
The financial implications of these improvements are significant, with many organizations reporting reduced operational costs alongside increased production capacity. The ability to dynamically adjust to changing demand patterns and product specifications further enhances the value proposition of AI-driven automation.
Enhancing Quality and Safety
Quality assurance processes benefit tremendously from AI's pattern recognition capabilities. Advanced vision systems can detect microscopic defects and subtle anomalies that challenge human inspectors. This heightened detection capability results in consistently higher product quality and compliance with rigorous aerospace standards.
From a safety perspective, automation reduces reliance on human operators for hazardous or repetitive tasks. Intelligent systems maintain consistent performance without fatigue-related errors, contributing to improved workplace safety records. The combination of enhanced quality control and reduced safety incidents creates a more robust manufacturing environment.
Optimizing Maintenance and Repair
The predictive capabilities of AI transform traditional maintenance approaches from reactive to proactive strategies. By analyzing equipment performance data, these systems can schedule maintenance activities during optimal windows, minimizing production disruption. This approach contrasts sharply with traditional methods that either wait for failures or perform maintenance on fixed schedules regardless of actual need.
When repairs become necessary, AI systems can recommend optimal procedures based on historical data and similar cases. This guidance helps technicians complete repairs more efficiently while minimizing the use of replacement parts and materials.
Improving Decision-Making and Forecasting
AI-powered analytics provide manufacturing leaders with unprecedented visibility into operations. Real-time dashboards and predictive models enable data-driven decisions regarding production planning, inventory management, and capital investments. These insights help organizations respond effectively to market fluctuations and evolving customer requirements.
Forecasting capabilities extend beyond immediate operational concerns to include long-term strategic planning. By analyzing market trends, customer demand patterns, and supply chain dynamics, AI systems help manufacturers make informed decisions about capacity expansion, product development, and resource allocation. This forward-looking perspective is particularly valuable in the aerospace sector where development cycles are lengthy and capital requirements are substantial.