Introduction to Aerospace Digital Twin Technology
Understanding the Concept of Digital Twins in Aerospace
Modern aerospace engineering has embraced an innovative approach called digital twin technology, which creates virtual counterparts of physical aircraft components like engines, airframes, or complete spacecraft systems. These sophisticated digital models precisely replicate the behavior and operational characteristics of their real-world equivalents, giving engineers unprecedented capabilities to track, evaluate, and enhance performance continuously. Through the fusion of sensor networks and computational modeling, Digital Twins enable anticipatory maintenance protocols and elevate safety benchmarks across aerospace operations.
At its core, a digital twin represents an evolving simulation that matures alongside the physical asset it mirrors. This dynamic model offers comprehensive visibility into equipment condition, operational metrics, and potential failure modes, empowering maintenance teams with proactive intervention capabilities. The technology has fundamentally transformed aircraft development, upkeep, and operational procedures, driving efficiency gains while minimizing service interruptions throughout the Aerospace sector.
Key Technologies Enabling Aerospace Digital Twins
The implementation of digital twins in aerospace depends on synergistic technologies including distributed sensor networks, large-scale data processing, cloud infrastructure, and machine intelligence. Embedded IoT sensors throughout aircraft systems generate continuous operational telemetry, which cloud platforms process to maintain accurate digital representations. These virtual models can simulate operational conditions with remarkable fidelity, enabling precise performance forecasting.
Machine learning advancements have particularly enhanced predictive capabilities, allowing aerospace firms to anticipate maintenance requirements and detect emerging issues before operational impacts occur. The convergence of these technologies creates an adaptive framework that continuously improves digital twin accuracy, establishing them as essential tools in contemporary aerospace engineering practice.
Applications of Digital Twin Technology in Aircraft Design
Digital twins serve as indispensable assets during aircraft development, enabling virtual prototyping and comprehensive system validation. Engineers leverage these models to evaluate aerodynamic properties, structural resilience, and integrated system behavior across diverse operating conditions - all without physical prototypes. This methodology dramatically compresses development timelines while yielding substantial cost efficiencies.
The technology facilitates rapid design iteration and optimization, allowing engineering teams to explore numerous configurations efficiently. These virtual environments promote cross-disciplinary collaboration by providing shared analytical platforms for evaluating design parameters, ultimately yielding aircraft that exceed rigorous industry safety and performance standards.
Enhancing Maintenance and Predictive Analytics with Digital Twins
Perhaps the most transformative application of digital twin technology lies in predictive maintenance strategies. Continuous monitoring through embedded sensor arrays provides real-time diagnostics for critical aircraft systems, enabling maintenance crews to detect anomalies early, plan interventions strategically, and prevent in-service failures.
This predictive approach not only reduces maintenance expenditures but also extends component service life. The resulting improvements in operational availability, reduced downtime, and enhanced safety margins have established digital twins as fundamental elements of modern aerospace maintenance programs.
The Future of Aerospace Digital Twin Technology
The ongoing evolution of digital twin capabilities promises to revolutionize aerospace operations through emerging technologies like cognitive computing, mixed reality interfaces, and decentralized processing architectures. Future implementations will feature greater autonomy, precision, and accessibility, enabling near-instantaneous decision-making that optimizes both flight performance and safety parameters.
As regulatory frameworks advance, digital twins will assume critical roles in aircraft certification processes and maintenance procedure validation. The integration of fleet-wide digital twin ecosystems will foster interconnected, intelligent aviation infrastructure, paving the way for safer, more sustainable global air transportation networks.
Key Applications of Digital Twins in Aerospace Manufacturing
Enhancing Design and Development Processes
Aerospace manufacturers utilize digital twins to generate precise virtual prototypes of aircraft systems and components, enabling iterative refinement without physical mockups. This methodology accelerates development cycles by facilitating comprehensive scenario testing and design optimization during early phases, yielding significant cost and time savings.
By incorporating Real-time data from sensor networks and historical test results, digital twins help identify potential design flaws during development. This predictive functionality ensures proactive resolution of engineering challenges, resulting in more reliable aircraft systems before manufacturing begins.
Optimizing Manufacturing Operations and Maintenance
Within production facilities, digital twins create dynamic representations of assembly processes, enabling Real-time Monitoring and optimization of manufacturing workflows. These virtual models help identify production bottlenecks, forecast equipment maintenance needs, and streamline operations - significantly boosting efficiency while reducing unplanned downtime.
The technology also enhances predictive maintenance strategies by analyzing continuous equipment sensor data. This allows maintenance teams to schedule interventions based on actual condition metrics rather than fixed intervals, preventing costly breakdowns while extending machinery service life - ultimately improving both productivity and workplace safety.
Supporting Flight Simulation and Pilot Training
Digital twins enable creation of highly realistic flight training environments that accurately replicate aircraft performance characteristics. These advanced simulators allow pilots to practice emergency procedures and complex maneuvers in risk-free settings, significantly reducing training costs while maintaining safety standards.
By updating digital twins with operational flight data, training programs can reflect current aircraft configurations and environmental conditions. This adaptive approach ensures pilots maintain proficiency across diverse operational scenarios, contributing to enhanced safety throughout the aviation industry.
Facilitating Lifecycle Management and End-of-Life Strategies
Digital twins support comprehensive asset lifecycle management by continuously tracking equipment condition and performance metrics. This holistic perspective enables optimized maintenance scheduling, upgrade planning, and eventual decommissioning strategies - reducing operational costs while minimizing environmental impact.
As aircraft components age, digital twins provide detailed wear analysis to inform replacement or refurbishment decisions. This proactive management approach maximizes operational efficiency throughout service life while supporting sustainable manufacturing practices through reduced material waste.
Enhancing Aircraft Maintenance and Lifecycle Management
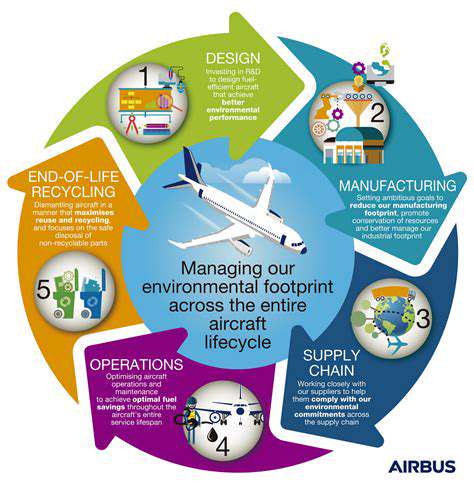
Implementing Advanced Diagnostic Technologies
Contemporary aircraft maintenance programs have been transformed by Advanced Diagnostic Technologies that provide continuous system monitoring capabilities. These innovations allow maintenance teams to detect potential issues during early stages, minimizing operational disruptions while enhancing safety margins. Sensor networks and analytical tools enable technicians to precisely locate developing problems, resulting in faster, more targeted repairs.
The integration of machine learning algorithms further enhances predictive maintenance strategies, enabling airlines to transition from reactive to proactive maintenance scheduling. This paradigm shift not only reduces operational interruptions but also delivers substantial long-term cost savings, making it essential for maintaining competitiveness in an industry where reliability and efficiency are critical.
Enhancing Training and Skill Development for Technicians
As aircraft systems grow increasingly complex, comprehensive training programs for maintenance personnel have become essential. Modern training methodologies incorporate virtual and augmented reality technologies to simulate realistic maintenance scenarios, providing technicians with practical experience in controlled environments. This immersive training accelerates competency development while ensuring technicians master current maintenance procedures and technologies.
Ongoing professional education and certification updates are equally vital to maintain technical proficiency amid rapid technological advancement. Airlines and maintenance providers must prioritize continuous skills development to ensure personnel can effectively service modern aircraft systems. Only through rigorous, ongoing training can maintenance teams uphold the aviation industry's exacting safety and reliability standards.
Optimizing Flight Operations and Safety Protocols

Implementing Advanced Flight Management Systems
Modern Flight Management Systems (FMS) are transforming airline operations by delivering real-time navigational data and flight optimization capabilities. These sophisticated systems integrate multiple data sources including satellite positioning and weather radar to optimize routes, improve fuel efficiency, and enhance safety parameters. Advanced computational algorithms enable more precise navigation and improved response to changing atmospheric conditions.
Airlines adopting cutting-edge FMS technology typically experience measurable improvements in schedule reliability and operational efficiency. The systems also improve coordination between flight crews and ground control, reducing communication errors and operational delays. Increased automation allows pilots to dedicate more attention to strategic decision-making, contributing to overall flight safety improvements.
Enhancing Crew Training and Simulation Programs
Comprehensive crew training remains fundamental to maintaining aviation safety standards and operational excellence. Airlines are increasingly utilizing high-fidelity simulation platforms that accurately replicate real-world flight conditions, enabling crews to practice emergency procedures and complex operational scenarios. This realistic training environment develops rapid decision-making skills and builds confidence in handling unexpected situations.
Advanced simulation systems can be customized to specific aircraft models and operational routes, ensuring crew members are thoroughly prepared for the unique challenges they may encounter. The result is safer, more reliable flight operations across entire airline fleets.
Continuous training and evaluation ensure crew members remain current with evolving safety protocols and technological developments. This commitment to ongoing education is essential for maintaining the highest levels of operational safety and performance in modern aviation.
Optimizing Scheduling and Crew Management
Effective crew scheduling represents a critical success factor in airline operations, directly impacting costs, employee satisfaction, and service quality. Airlines now utilize advanced scheduling software that considers multiple variables including crew availability, regulatory rest requirements, and operational demands to create optimal work rotations. This automated approach minimizes human error while ensuring full regulatory compliance, reducing delays and cancellations.
By analyzing historical patterns and real-time operational data, airlines can proactively adjust schedules to accommodate disruptions like weather events or technical issues. Effective fatigue management through proper rest scheduling remains essential for maintaining crew performance and safety standards.
Modern scheduling tools enable more efficient resource allocation, allowing airlines to respond effectively to market fluctuations and seasonal demand variations. The result is improved operational profitability alongside enhanced crew satisfaction through more predictable and equitable scheduling practices.
Integrating Data Analytics and Predictive Maintenance
Data analytics has become indispensable in contemporary aviation operations, providing insights that drive continuous improvement. Airlines collect extensive operational data from aircraft systems, maintenance records, and flight operations, which analytical tools process to identify trends and anomalies. This proactive analytical approach enables predictive maintenance strategies, reducing unexpected equipment failures and operational disruptions.
Predictive models forecast potential component issues before they occur, allowing maintenance during planned ground times rather than emergency repairs. This methodology increases aircraft availability while extending the operational life of critical components, ultimately reducing maintenance expenditures.
Beyond maintenance applications, data analytics supports route optimization, fuel management, and crew scheduling - contributing to more efficient overall operations. As artificial intelligence and machine learning technologies advance, their integration will further enhance predictive capabilities, shaping the future of aviation operations management.